Warehouse management systems (WMS) have revolutionised the way businesses manage their inventory and supply chains. These systems have helped increase efficiency and reduce costs by automating and optimising warehouse processes. In this article, we will focus specifically on how warehouse management systems can help increase efficiency in a warehouse, with a particular focus on order-picking efficiency.
Order picking is the process of selecting and gathering products from a warehouse to fulfil customer orders. This process can be time-consuming and labour-intensive, and mistakes can be costly. Therefore, optimising order-picking efficiency is crucial for warehouse operations. Here are some ways that warehouse management systems can help improve order-picking efficiency:
- Automation: Warehouse management systems can automate the order-picking process by using barcode scanners, voice recognition technology, and other technologies to guide workers to the correct locations and items. This reduces the risk of errors and increases the speed of the process.
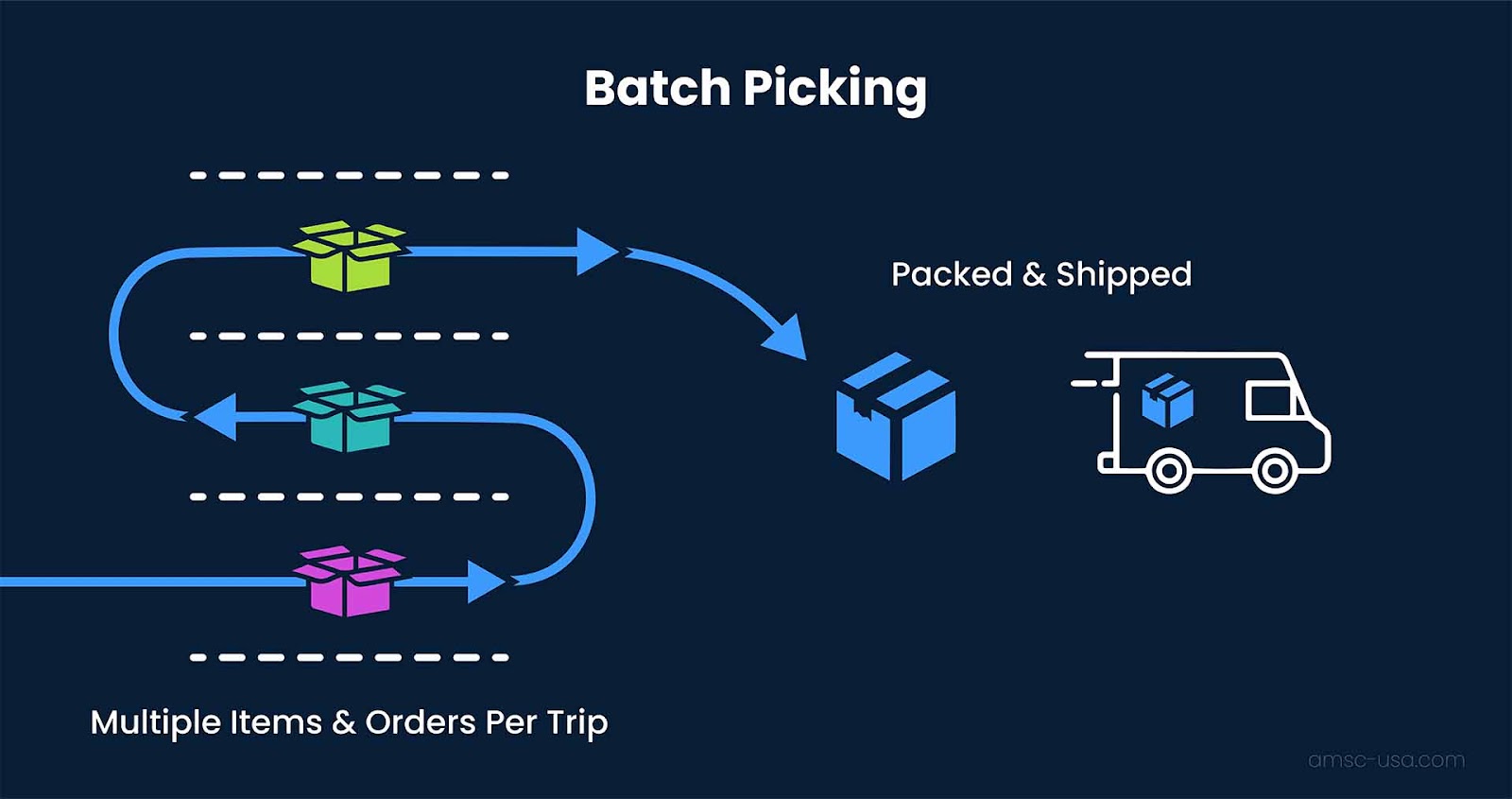
- Batch Picking: Batch picking is the process of selecting multiple orders at once rather than one order at a time. Warehouse management systems can help optimise batch picking by grouping orders with common items or locations, reducing travel time and increasing the efficiency of the process.
- Zone Picking: Zone picking is the process of assigning workers to specific zones in the warehouse and having them pick only the items in their designated zones. This reduces the amount of travel time and increases the efficiency of the process. Warehouse management systems can help optimise zone picking by assigning workers based on their skills and experience and tracking their progress to ensure they meet their targets.
- Pick-to-Light: Pick-to-Light is a technology that uses lights and displays to guide workers to the correct locations and items. This technology is particularly useful for high-volume, low-variety goods, as it reduces the risk of errors and increases the speed of the process.
For all these processes to come together well, the layout of the warehouse matters.
Warehouse Layouts
A well-designed warehouse layout is crucial for efficient warehouse operations. There are several warehouse layouts, each with advantages and disadvantages. Here are some of the most common warehouse layouts:
- Flow-Through Layout: In this layout, goods are received at one end of the warehouse and moved straight to the other end, where they are shipped out. This layout is ideal for high-volume, low-variety goods, as it maximises the flow of goods and minimises the need for storage space.
- Cross-Docking Layout: In this layout, goods are received and sorted into outbound trucks without being stored in the warehouse. This layout is ideal for companies that receive and ship large quantities of goods daily, such as grocery distributors.
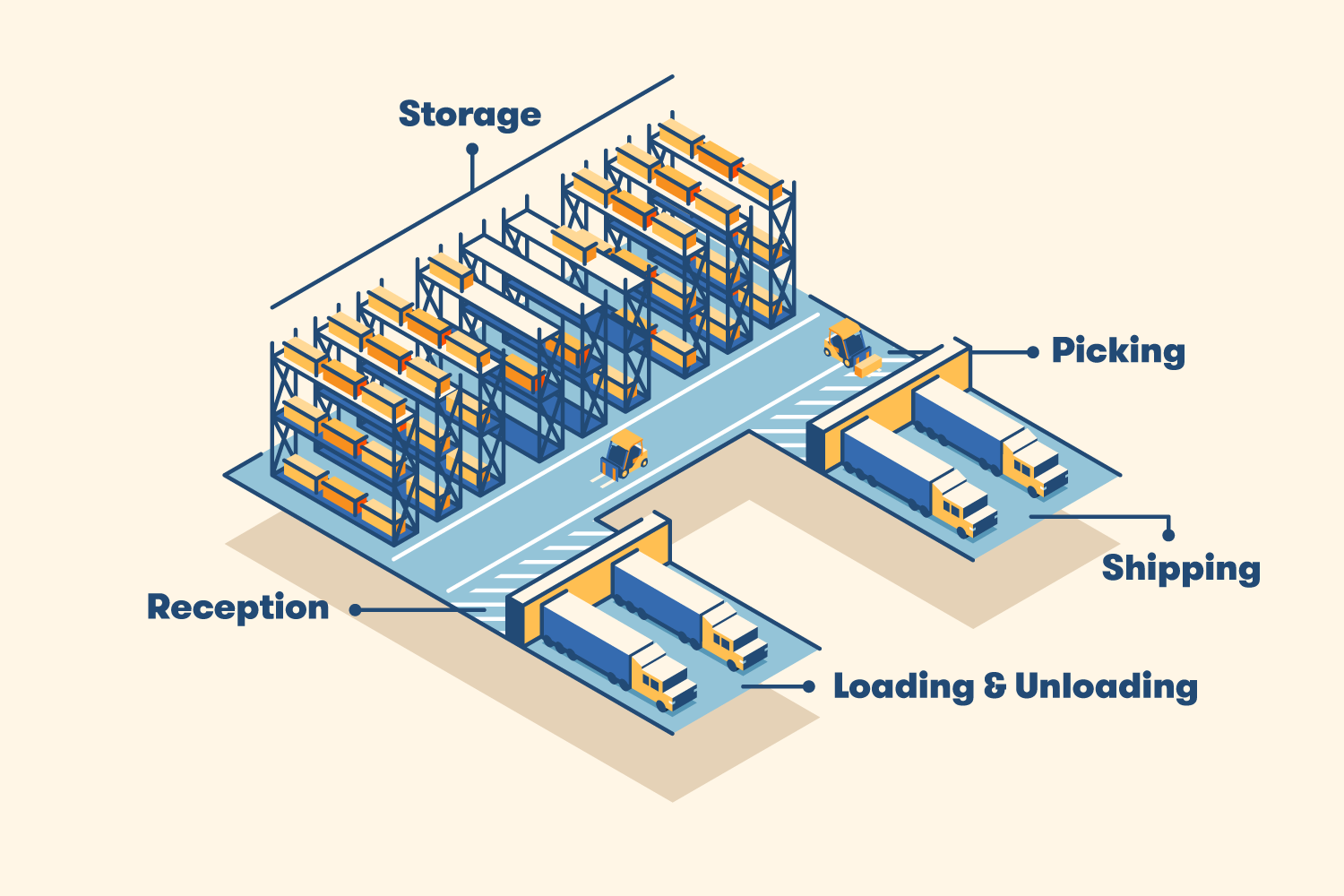
- U-Shaped Layout: In this layout, goods are received at one end of the warehouse and moved in a U-shape to the other, where they are shipped out. This layout is ideal for companies that need to process goods quickly and efficiently, as it allows for a continuous flow of goods.
- Zoned Layout: In this layout, the warehouse is divided into different zones based on the type of goods stored. Each zone has its receiving, storage, and shipping areas, allowing for efficient and organised handling of goods.
Each type of warehouse layout has its advantages and disadvantages, and the ideal layout will depend on the specific needs of each company. However, regardless of the type of layout used, a well-designed warehouse layout will help reduce unnecessary movement and increase the flow of goods, resulting in increased efficiency.
New Developments in Order Picking
Several new developments in order picking are helping increase efficiency in warehouses. Here are some of the most significant developments:
- Robotics: Robotics technology is becoming increasingly common in warehouses, particularly for order picking. Robots can pick items from shelves and transport them to the shipping area, reducing the amount of manual labour required and increasing efficiency. Warehouse management systems can integrate with robotics technology to optimise the order-picking process, ensuring that robots are used in the most efficient way possible.
- Artificial Intelligence: Artificial intelligence (AI) optimises the order-picking process by analysing data and identifying patterns. AI can help identify the most efficient order-picking routes, predict inventory levels, and optimise worker assignments, increasing efficiency and reducing costs.
- Augmented Reality: Augmented reality technology guides workers through order picking by overlaying digital information onto the real world. This technology can help reduce errors and increase efficiency by providing workers with real-time information about the items they pick and their locations.
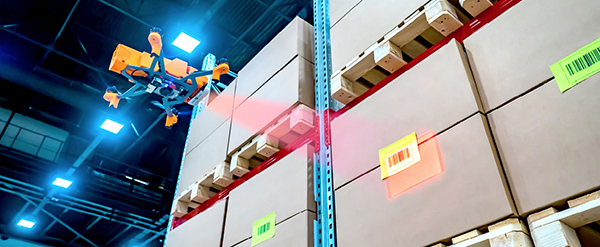
- Drones: Drones are used in warehouses to quickly and efficiently transport small items, reducing the time required for order picking and increasing efficiency. Warehouse management systems can integrate with drone technology to optimise the order-picking process, ensuring that drones are used in the most efficient way possible.
In conclusion, warehouse management systems have revolutionised the way businesses manage their inventory and supply chains, helping increase efficiency and reduce costs. By optimising warehouse layouts and order-picking processes, companies can reduce unnecessary movement, increase the flow of goods, and reduce the risk of errors, resulting in increased efficiency and reduced costs.
With the new developments in order-picking technology, such as robotics, artificial intelligence, augmented reality, and drones, the potential for increased efficiency will only grow, making warehouse management systems an essential tool for businesses that want to remain competitive in today’s fast-paced economy.