As the world becomes increasingly connected and e-commerce continues to grow, customers have come to expect fast and reliable shipping times. In fact, according to a recent survey, nearly two-thirds of online shoppers expect orders to be delivered within two days, and more than a third expect same-day delivery. This presents a significant challenge for businesses that rely on warehousing and distribution to fulfil customer orders.
Meeting these demands can be difficult, but it’s possible. Warehouse management systems (WMS) can play a crucial role in helping companies to optimise their operations and improve shipping times. The benefits of warehouse systems can be mainly applied to three broad categories:
- Inventory Storage and control
- Warehouse layout and picking efficiency
- Shipping Accuracy
The Role of WMS in Improving Inventory Control
One of the key benefits of WMS is improved inventory control. By providing real-time information on inventory levels and order status, WMS can help to ensure that items are available for immediate fulfilment. A WMS can also help prevent stockouts, delayed shipments and dissatisfied customers. By providing real-time data on inventory levels, WMS can alert warehouse managers when stock levels are low, allowing them to reorder items on time.
In addition, WMS can help to improve inventory accuracy. By providing real-time updates on inventory levels, WMS can help to reduce errors such as overstocking or understocking. This can reduce the time required to locate and prepare items for shipping, allowing companies to fulfil orders more quickly.
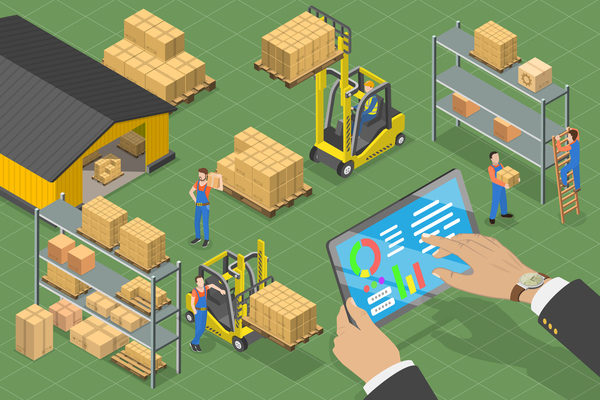
The Role of WMS in Improving Order Picking Efficiency
Another important benefit of WMS is improved order-picking efficiency. By automating tasks such as order allocation and picking, WMS can reduce the time and labour required. This can result in faster order processing times and reduced labour costs. WMS can also help reduce the time required to locate items for picking. By providing real-time data on inventory locations, WMS can reduce the time needed to locate items for picking, allowing companies to fulfil orders more quickly.
In addition, WMS can help to improve order accuracy. By providing real-time data on order status, WMS can help to ensure that the correct items and quantities are picked for each order. This improves shipping accuracy as well.
The Role of WMS in Improving Shipping Accuracy
Reducing errors in order items, be it type or quantity, can improve customer satisfaction and reduce the cost of returns and exchanges. In addition, WMS can help to improve the accuracy of shipping labels and documentation. By providing real-time data on order status, WMS can help to ensure that the correct shipping labels and documentation are generated for each order. This can help to reduce shipping errors and improve customer satisfaction.
A WMS can provide valuable insights into warehouse operations through real-time reporting and analytics. By tracking key performance indicators such as order cycle time and inventory turnover, WMS can help warehouse managers identify areas for improvement and make data-driven decisions. This can help to optimise operations and further improve shipping times.
In conclusion, warehouse management systems help companies meet the growing demand for faster and more reliable shipping times. By improving inventory control, order picking efficiency, shipping accuracy, and warehouse layout, WMS can help companies optimise their operations and improve shipping times. As such, WMS has become an essential tool for any company that relies on warehousing and distribution to meet customer demand in the fast-paced world of e-commerce.